In today's era of rapidly advancing electronic technology, the integration density of Printed Circuit Board Assemblies (PCBAs) is continually increasing, while component sizes are shrinking, and layouts are becoming progressively denser. This trend significantly heightens the susceptibility of PCBAs to their operating environment. What was once considered an "optional" protective measure has now become an essential cornerstone for ensuring the long-term stable operation of electronic products in complex and variable environments—this is the PCBA conformal coating process. It is not merely a procedural step but a testament to the ingenuity within electronic manufacturing for addressing harsh environmental challenges and enhancing core competitiveness.
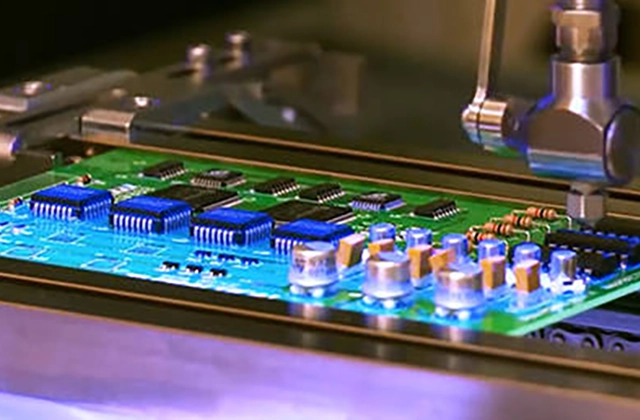
PCBA processing cleaning
Why is Conformal Coating So Necessary? Invisible Threats from the Environment
Throughout their lifecycle, electronic products are perpetually exposed to potential environmental threats. Any electronic product faces the risk of failure due to factors such as humidity, dust, chemical corrosion, temperature fluctuations, and mechanical stress. These "invisible threats" are potent enough to devastate meticulously designed circuits:
Pervasive Moisture and Water Vapor: The Primary Enemy of Reliability
- Mechanism of Harm: Water molecules are exceedingly small and can easily permeate the interstices of certain polymeric materials or pinholes in coatings, reaching the underlying metal of the PCBA. When relative humidity (RH) is high, a thicker adsorbed water film forms on material surfaces, which, in conjunction with contaminants (such as flux residues and salts), creates a conductive electrolyte. Under an electric field, this readily triggers Electrochemical Migration (ECM), leading to the formation of dendritic conductive paths of metal ions across the insulating substrate, causing short circuits. Furthermore, moisture can lead to increased leakage currents and signal distortion in high-frequency circuits.
- Scenario Manifestation: Appliances in humid southern monsoon seasons, outdoor surveillance equipment, bathroom electronics, and even devices experiencing "dew point" condensation due to temperature changes, all face severe moisture challenges. Therefore, moisture protection is a primary step in safeguarding products, and conformal coatings provide an effective moisture barrier.
Ubiquitous Dust: The Cumulative Effect Not to Be Underestimated
- Mechanism of Harm: Atmospheric dust, particularly fine particulate matter smaller than 2.5 microns in diameter, readily adsorbs ionic contaminants and settles on PCBA surfaces. This accumulated dust not only can impair connector contacts but, more critically, becomes a breeding ground for electrochemical corrosion in humid conditions, significantly increasing failure rates.
- Scenario Manifestation: Industrial control equipment, mining operation machinery, and communication base stations continuously exposed to the atmosphere. In these environments, dust protection is equally critical for ensuring the long-term stable operation of products, and conformal coatings effectively encapsulate circuitry, preventing dust ingress.
Highly Corrosive Salt Spray: The Nightmare of Coastal and Special Industrial Environments
- Mechanism of Harm: Salt spray (primarily composed of sodium chloride, etc.) is highly corrosive, capable of rapidly degrading the plating on metal components and drastically accelerating electrochemical corrosion, leading to conductor breakage and component failure. Similar corrosive agents include hand perspiration (containing salts, lactic acid, etc.) and improperly cleaned halogenated or acidic flux residues.
- Scenario Manifestation: Marine equipment, outdoor electronic installations in coastal regions, and equipment near chemical plants. In these areas, protection against salt spray is a decisive factor in product survivability, making the chemically inert protective layer provided by conformal coatings crucial.
Stealthily Proliferating Mold and Fungus: The Destroyer of Organic Materials
- Mechanism of Harm: In warm, humid conditions, mold and fungus can proliferate on PCBA surfaces, especially on organic material portions. Their growth not only consumes organic materials, degrading insulation properties, but their metabolic byproducts (organic acids) can further corrode circuitry, impairing insulation and dielectric strength, and even inducing arcing.
- Scenario Manifestation: Equipment used in tropical rainforests, spare parts stored long-term in damp warehouses, and agricultural machinery. Protection against mold and fungus is indispensable for maintaining the electrical performance and physical integrity of PCBAs, and conformal coatings can inhibit the conditions conducive to their growth.
In summary, the potential harm to PCBAs from environmental factors such as humidity, dust, salt spray, and mold/fungus is substantial and multifaceted. Conformal coating, by forming a tough, dense, and insulating protective film on the PCBA surface, effectively isolates sensitive electronic components from these adverse environments, thereby fundamentally enhancing product reliability, safety, and operational lifespan. This is no longer a mere "nice-to-have" but an indispensable requirement for the design of modern high-reliability electronic products.
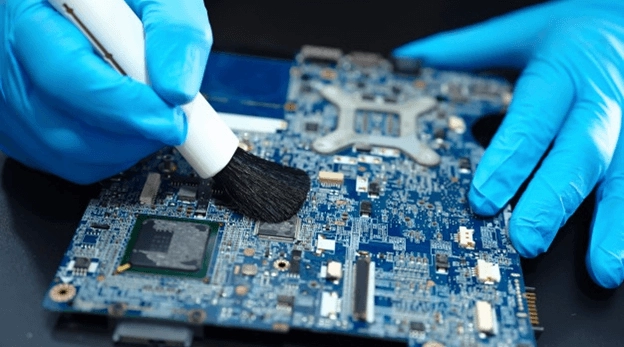
PCB Cleaning Board
The Process Ingenuity of Conformal Coating: Tailored to Needs and Board Specifics
The conformal coating process is not monolithic; its sophistication lies in the ability to flexibly select and combine different application methods and materials (such as acrylics, polyurethanes, silicones, UV-curable coatings, etc.) based on PCBA complexity, production volume requirements, cost considerations, and the precision requirements for specific protected areas.
Core Process Steps: Cleaning → (Masking) → (Pre-baking/Dehumidification) → Application → Leveling/Flow-out → Curing → Inspection → (De-masking)
Scenario-Based Demonstration of Process Necessity and Sophistication:
Scenario 1: R&D Prototyping, Small-Batch Repair, or Localized Touch-up – The Flexibility of Manual Brushing
Necessity Manifestation: During R&D, when PCBA designs are frequently altered, or after repairing a faulty PCBA, rapid, small-area protection is needed. Investing in large-scale automated equipment is neither economical nor practical at this stage.
Process Sophistication: Manual brushing, with its extremely low equipment cost and high flexibility, perfectly meets such demands. Operators can precisely control the application area, avoiding contamination of non-coated parts (e.g., connectors, test points). Although uniformity and efficiency are limited, its precision application capability and minimal material wastage make it an indispensable auxiliary method.
Scenario 2: Medium-Volume Production, Certain Uniformity Requirements – The Balance of Manual Spraying
Necessity Manifestation: When production volume increases and there are requirements for coating appearance and basic protective performance, the efficiency and consistency of brushing become inadequate.
Process Sophistication: Manual spraying (using a spray gun) achieves a more uniform coating and higher efficiency compared to brushing. Skilled operators can effectively cover PCBAs of various shapes. Although detailed masking is still required to protect restricted areas, it strikes a good balance between cost and effectiveness.
Scenario 3: High-Volume Production, High-Density Complex PCBAs, Numerous Restricted Areas – The Precision and Efficiency of Selective Automated Coating
Necessity Manifestation: PCBAs in modern consumer electronics, automotive electronics, and communication equipment are often densely populated with components, featuring numerous and irregularly shaped restricted areas such as connectors, test points, and thermal interfaces. Traditional manual masking is time-consuming, labor-intensive, and prone to errors, severely impacting production efficiency and quality.
Process Sophistication: Selective coating equipment (e.g., XYZ or multi-axis robotic systems employing precision dispensing valves) represents the pinnacle of this process ingenuity.
- Precision: Through pre-programmed routines, the dispensing head accurately avoids restricted areas, applying coating only to areas requiring protection. Its edge definition control capability ensures clean coating boundaries.
- Efficiency: Significantly reduces or even eliminates manual masking and de-masking steps, markedly improving production throughput.
- Consistency: Automated operation ensures high consistency in coating thickness and coverage for every board, complying with standards like IPC-A-610E regarding coating thickness (typically 25-150 microns, varying by coating type) and coverage.
- Material Savings: On-demand dispensing minimizes conformal coating wastage.
This "intelligent" application method perfectly addresses the protection challenges of high-density, complex PCBAs and is an inevitable choice for modern large-scale electronic manufacturing.
Scenario 4: Specific High-Reliability Requirements, Comprehensive Defect-Free Protection – The Ultimate Pursuit with Dip Coating or Vapor Deposition (e.g., Parylene)
Necessity Manifestation: For applications demanding extreme reliability, such as aerospace, medical implants, and deep-sea exploration, any minute defect can lead to catastrophic consequences. A uniform, dense, pinhole-free coating capable of covering all complex surfaces is required.
Process Sophistication:
- Dip Coating: By immersing the entire PCBA into a coating bath and slowly withdrawing it, a very uniform coating can be achieved with excellent coverage of complex geometries. Key parameters include controlling the coating viscosity and withdrawal speed to prevent air bubbles and sagging.
- Parylene Vapor Deposition: This is an even more advanced process. In a vacuum environment, it forms an ultra-thin (potentially down to micron or even sub-micron levels), highly uniform, pinhole-free conformal coating directly on the PCBA surface via vapor phase monomer polymerization. It offers outstanding protective performance and biocompatibility. Although the equipment is expensive and the process complex, its value is irreplaceable in scenarios pursuing top-tier protection.
Leveraging UV Curing Technology: Enhancing Speed and Environmental Friendliness
Necessity Manifestation: In today's pursuit of production efficiency and environmental protection, the long curing times and VOC (Volatile Organic Compound) emissions of traditional solvent-based conformal coatings have become bottlenecks.
Process Sophistication: The advent of UV-curable conformal coatings, in conjunction with UV curing ovens, enables curing within seconds, drastically boosting production efficiency. Concurrently, UV coatings are often 100% solids or low-VOC, making them more environmentally friendly. For areas shadowed from UV light, dual-cure mechanisms (e.g., UV + moisture or UV + thermal) are typically employed to ensure comprehensive curing.
Indispensable Pre- and Post-Application Safeguards
The sophistication of the process is not only evident in the application itself but also in a complete, closed-loop workflow:
- Thorough Cleaning and Pre-baking/Dehumidification: This is fundamental to ensuring the adhesion and protective efficacy of the conformal coating. Contaminants and residual moisture are the primary culprits for under-coating corrosion. Pre-baking temperature/time schedules (like those found in technical guidelines or specific material datasheets) are practical guides to ensure PCBAs are in optimal condition before coating.
- Stringent Inspection: Ensures coating quality through methods such as visual inspection (for bubbles, pinholes, orange peel effect, sagging, cracking, foreign matter, etc.), thickness measurement (using micrometers or dry/wet film thickness gauges to ensure compliance with standards like IPC-CC-830B), and UV light inspection (using fluorescent tracers to check coverage uniformity).
The Outlook for PCBA Coating
The PCBA conformal coating process, having evolved from an initial response to basic environmental protection needs into a complex systems engineering feat integrating materials science, precision mechanics, and automation control, has an undeniable "necessity." It does more than just provide a "protective garment" for PCBAs; through ingenious process design and flexible application adaptation, it offers a solid guarantee for the stable and reliable operation of modern electronic products in increasingly harsh environments, fully embodying the relentless pursuit of excellence in electronic manufacturing. In the future, as electronic products advance towards higher integration densities and more extreme application environments, the importance of conformal coating technology will undoubtedly continue to grow.